45 South Cherry Packhouse wastewater disposal system Cromwell
May Plumbing & Gas was approached by the owners when the current septic system had failed at the site.
The packhouse and orchard operations employ 350 staff at the peak of their season and there is onsite camping facilities as well as a 50-bed hostel.
We carried out investigations and feasibility on options for replacement or construction of a pumped reticulation system to connect to the Cromwell town sewer system.
We engaged engineers to design an industrial wastewater treatment plant to our requirements.
The plant was significant, consisting of 5 x 20,000-litre concrete tanks buried which made up each stage of the system. There were several existing septic tanks on site which were decommissioned and new civil drainage was installed on the factory site to convey all wastewater to the new treatment plant. The system has telemetry to enable online monitoring and report to the regional council.
We advised the client that in order to keep the septic system output below the allowable level that we could use some of the existing infrastructure and pipe greywater to this which can be disposed of to ground, so the commercial laundry on site which produces a lot of wastewater was treated in this way thereby reducing the load on the treatment plant.
Low water use toilet cisterns and flow restrictors on showers were installed also.
The following year
The following year, the client advised they were building a workshop – not much plumbing, just a toilet and some washbasins. The building was 1200 square metres, the stormwater runoff from this roof was enormous, so we designed and installed a disposal system to cope with the flow consisting of civil drainage, washdown pads, surface water collection sumps and two soak pits, each one 50 cubic metres in capacity.
An oil and grease interceptor trap was installed for the vehicle and equipment wash down area.
We designed and constructed water filling stations for the orchard spray tank filling complete with backflow prevention systems. We also fitted a toilet and some washbasins.
The next project
The next project on-site was to address the ageing water infrastructure and the rapid growth of the company and the factory output. We were given a brief of what was desired and set about designing the system.
A new larger water main connection was installed, an industrial RPZ boundary device installed, new 100mm water mains run to the factory and new water mains run around to the various buildings on site, several backflow preventers installed at high-risk areas, including chemical spray tank filling stations. The company was installing a new packhouse system which used a 40 000 litre water tank.
That tank used to take several hours to fill each night during production, now it takes 20 minutes.
All of the above projects were designed and built by May Plumbing & Gas.
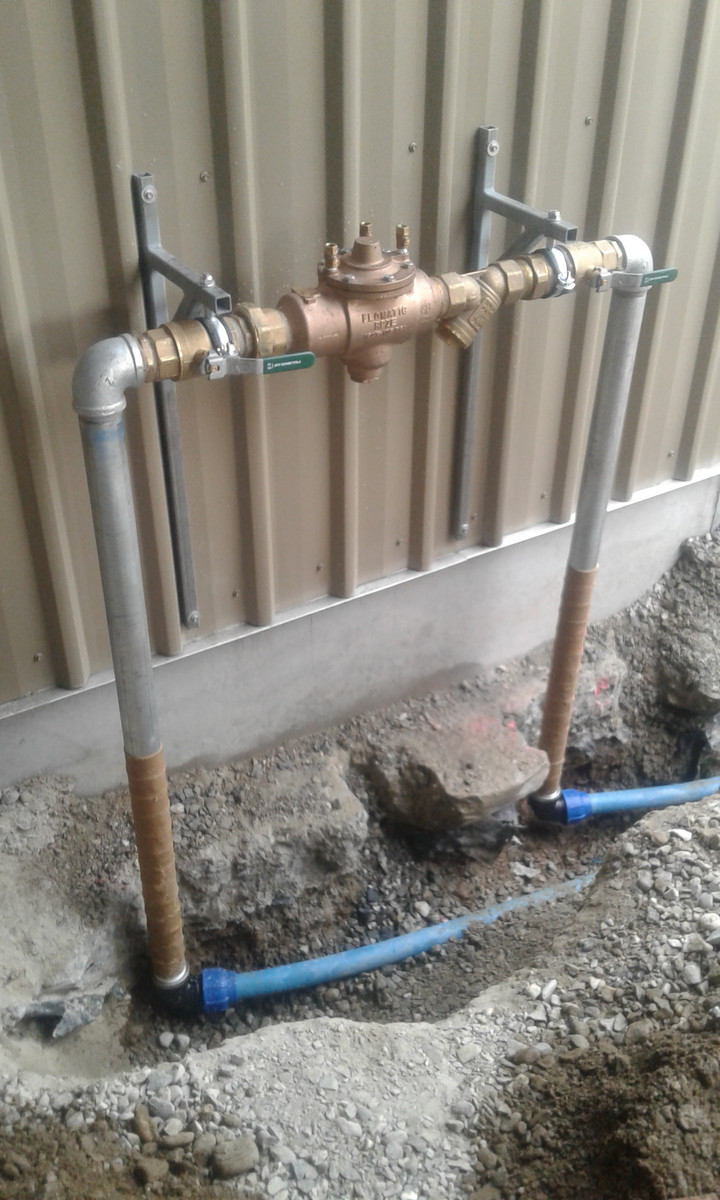
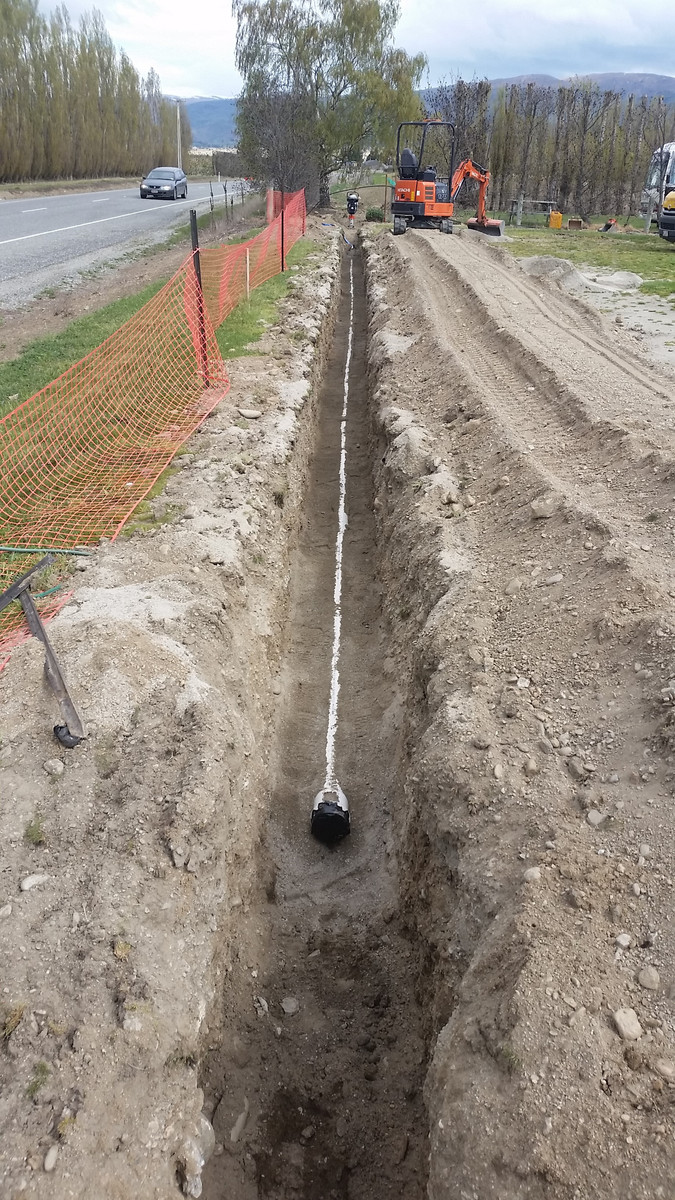
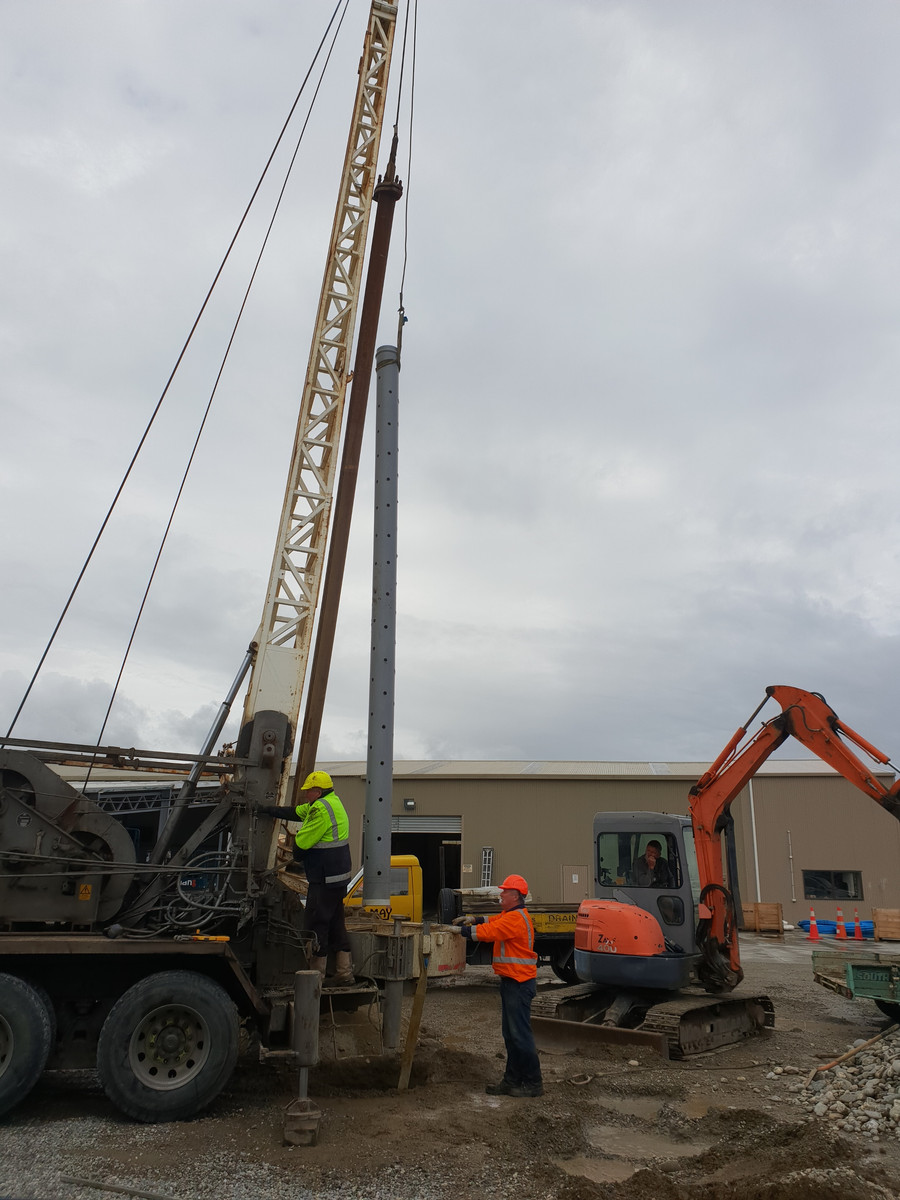
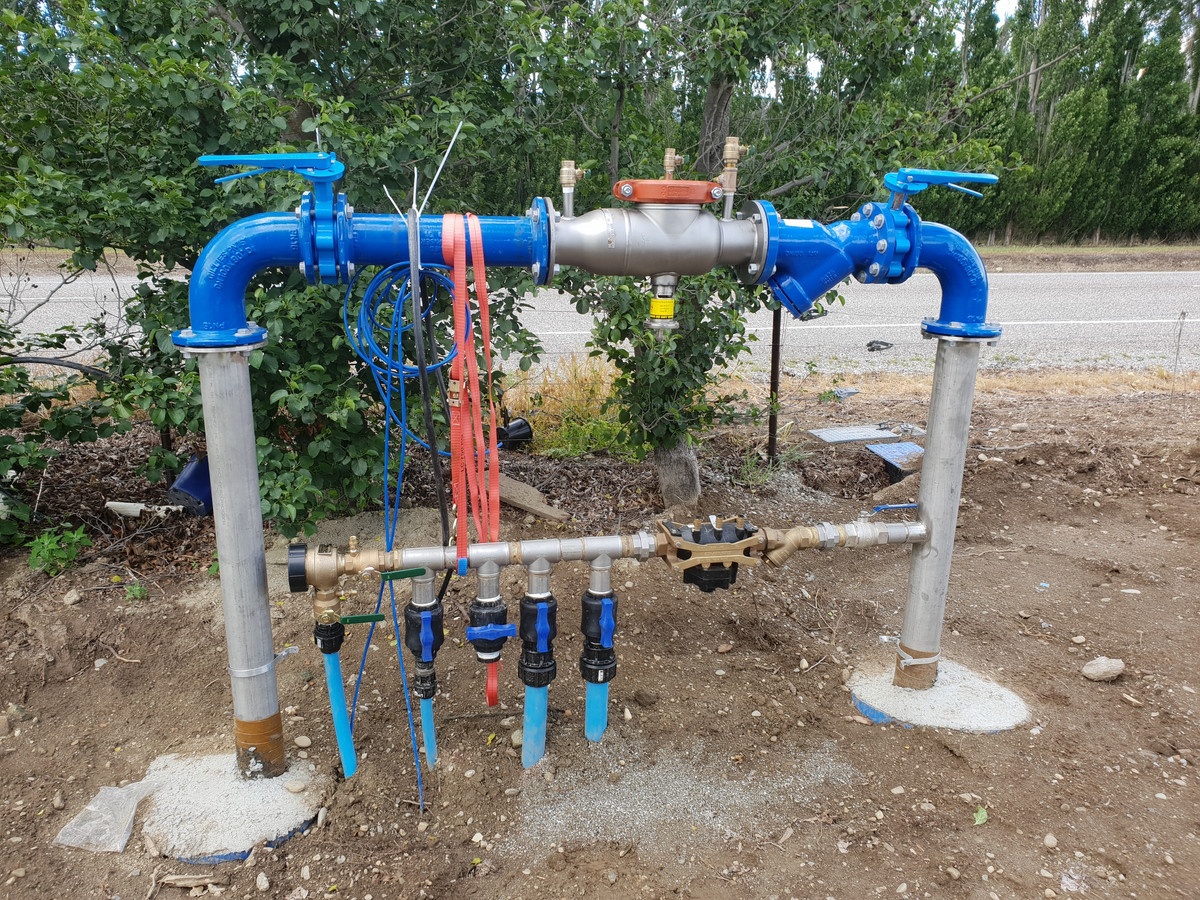
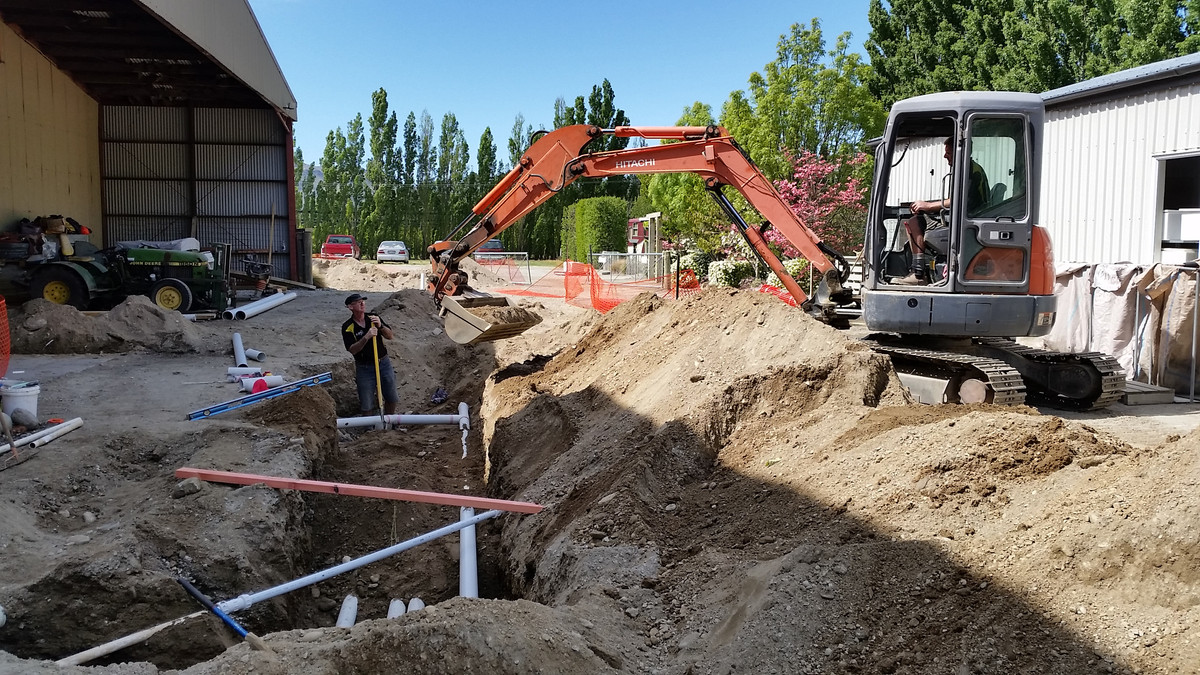
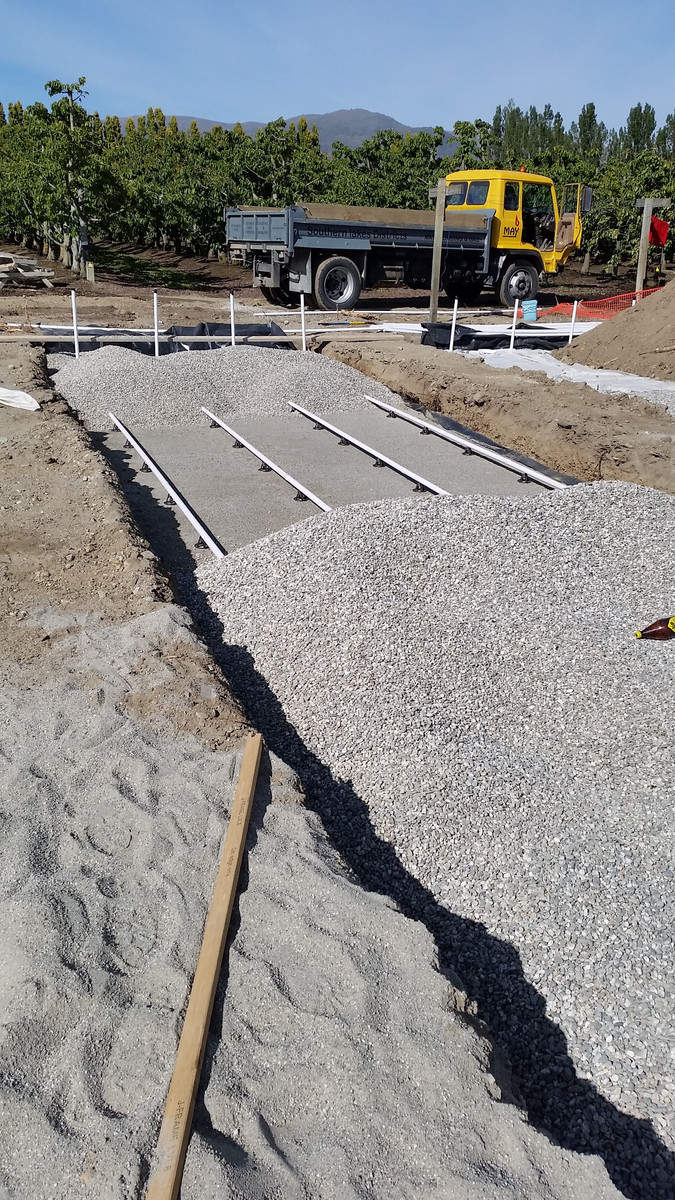
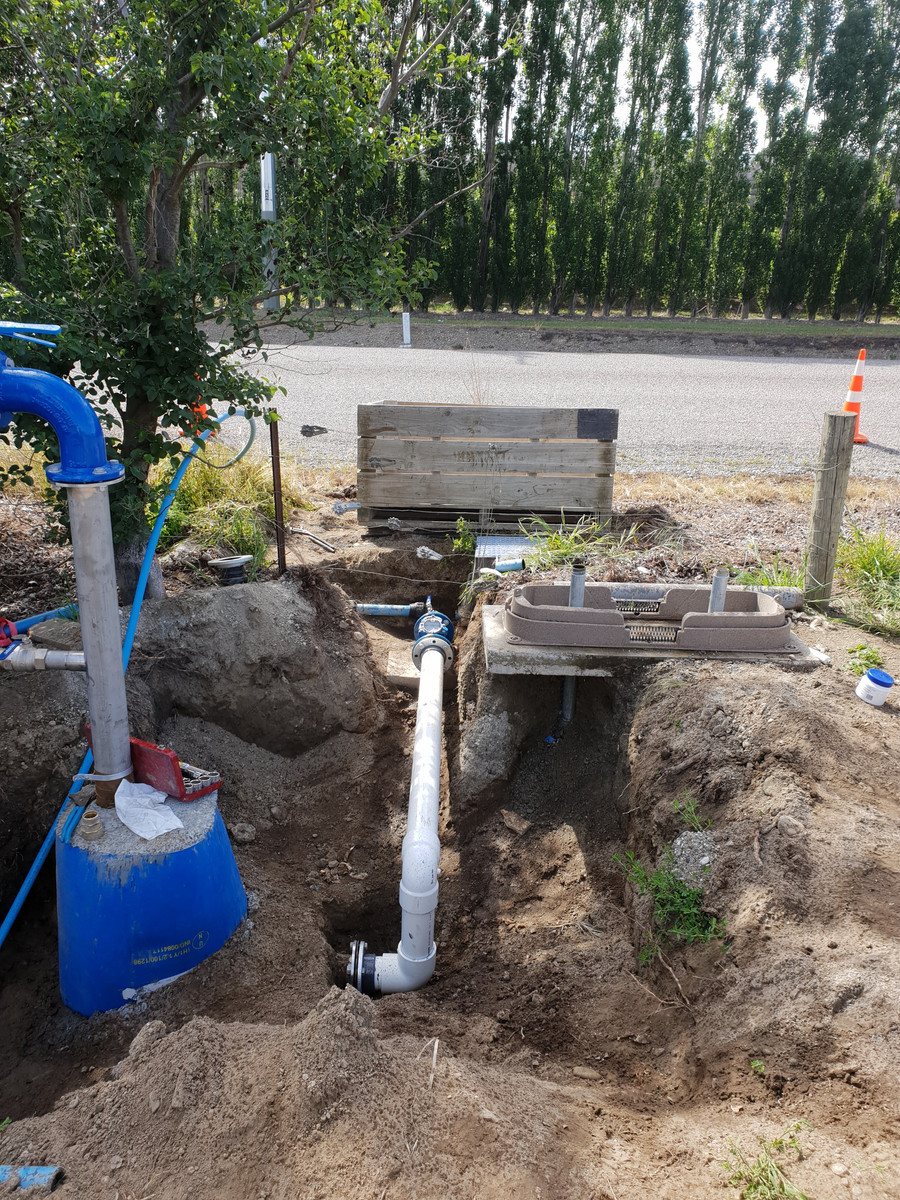
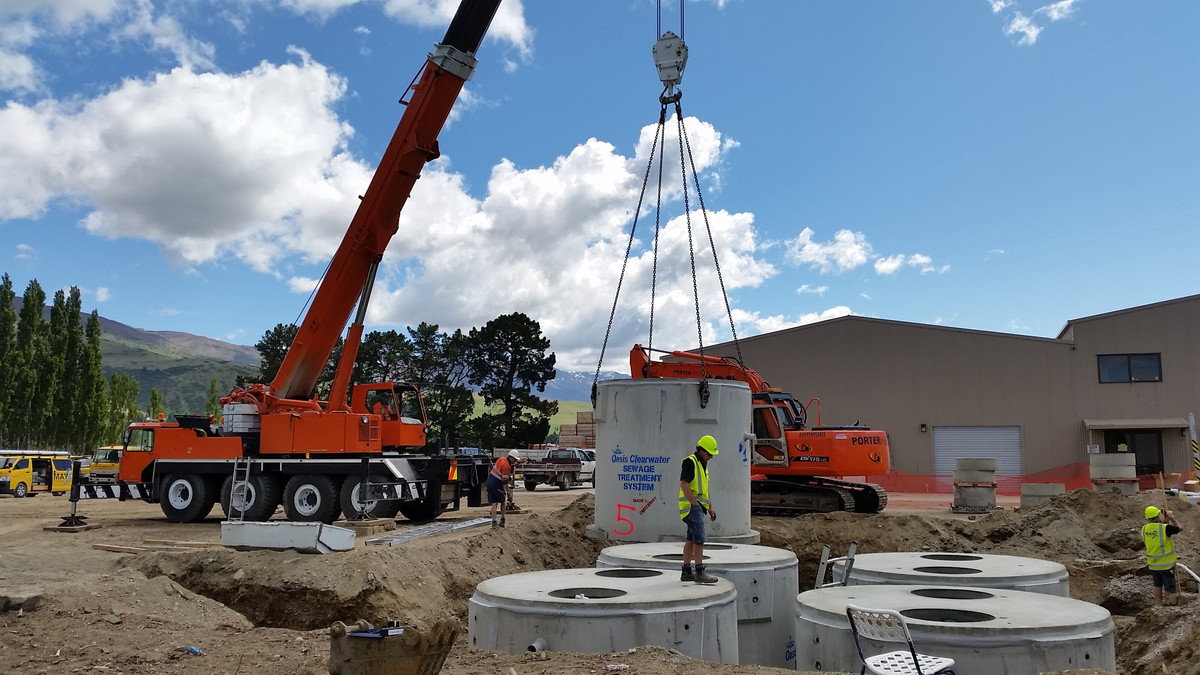